Inspection of returned crates
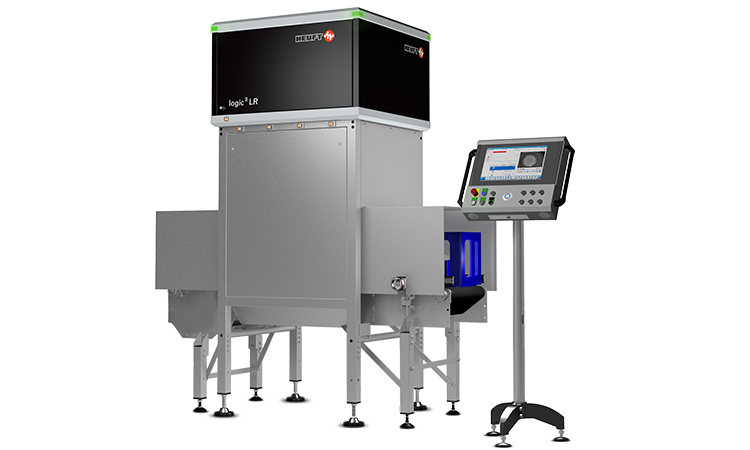
HEUFT logic II LR
Sorting out non-brand bottles and establishing brand purity: the inspection of bottle crates.
The HEUFT logic II LR empty container inspection system ensures that non-brand, contaminated, and damaged bottles and warped crates do not enter production. The integrated majority detection controls the maximum share of these. Therefore the HEUFT logic II LR optimises line efficiency and reduces production costs sustainably.
Top-down inspection
Ensuring unpacking suitability and safety: checking the compartments and the handling grips.
Foreign objects, top-down bottles and faulty handgrip areas: the HEUFT logic II LR finds returned returnable bottle crates with such faults reliably. It checks their complete insides from above using the powerful HEUFT reflexx A.I. camera for this.
Read more...
Each individual compartment is examined so that crates containing lying containers, top-down bottles or foreign objects are clearly identified and specifically rejected. This ensures the unpacking suitability of the crate. The detection of missing or broken handling grips prevents the risk of injuries. Thus the HEUFT logic II LR upholds the efficiency of the complete line as well as product safety.
Fullscreen
Closure, shape and colour check
Finding non-brand bottles: identifying mixed up crates.
Correct brand, safe and efficient: the HEUFT logic II LR identifies mixed up crates and therefore protects against standstills, bottlenecks and productivity losses.
Read more...
Intelligent evaluation methods detect closures and find bottles of the wrong color. The empty container inspector even reliably distinguishes between different types of swing-top bottles – regardless of whether their closures are open or still on the bottle. With homogeneous lighting from below and powerful camera technology, it finds bottles of the wrong color. Special HEUFT reflexx A.I. cameras are used to clearly distinguish between glass and PET. The image processing determines the number of non-brand containers and decides whether the crate is rejected based on individually adjustable parameters. This prevents too many non-brand bottles from entering the line and only being removed from circulation by the empty bottle sorting unit or the empty bottle inspector.
Fullscreen
Checking the height proportions
Always at the correct height: profile measurement.
Distorted compartments, foreign objects under the bottle, broken or deformed containers: different factors result in deviating height proportions in the crate. Various factors lead to different height ratios in the box. The HEUFT logic II LR registers them with a 3D scan. The laser can examine different returned crates with empty bottles continuously. It is so flexible in the course of this that it does not have to be readjusted each time for brand and program changes.
Fullscreen
Checking the dimensions
Identifying distorted crates reliably: checking the crate geometry.
Non-brand, faulty and distorted: the HEUFT logic II LR sorts out bottle crates reliably which are not suitable for reuse because they do not belong to the current production program or cannot be unpacked.
Read more...
It determines the length of the diagonals of the crate and uncovers deviations to the target geometry for this. Length, width and height are checked at the same time and compared to stored reference values. The bottle crate in question is rejected before it can enter the line if they differ considerably from the ideal dimensions.
Colour and logo detection
Showing their colours: checking the brand affiliation.
Detecting, comparing and keeping apart: the ever-increasing diversity of brands also affects the outer packaging. Colour and design are an important distinguishing criterion at the Point of Sale (POS). The HEUFT logic II LR checks the colouration of the crate colour and logos in order to make sure that the correct bottles are in the correct crate.
Read more...
It photographs the relevant area using a HEUFT reflexx A.I. camera. The intelligent HEUFT reflexx A.I. image processingevaluates the photograph and compares it in real time with the stored reference sample. The result: a homogeneous supply of the appropriate empty crates.
Combined evaluation of all the measuring results
Calculating the total probability: analysis by means of fuzzy logic.
Combining, comparing and judging: different measuring procedures only produce an optimal result when they are linked with each other. After all not all the crates should be sorted out. Even those with inconclusive, borderline properties can indeed be the correct ones.
Read more...
That is why the fuzzy logic calculates the probability of the individual values determined with regard to brand affiliation and combines them via a complex algorithm into the total probability. Therefore empty crates of the correct brand with negligible deviations do not have to be sorted out. This has a positive effect on the efficiency and productivity of the complete line for returnables.
Complete inspection of empty crates
Detecting deformations, broken handles and shelves, foreign objects in the compartments: empty crate inspection for perfect condition.
A true all-rounder. When positioned behind the can washer, the HEUFT logic II LR inspects empty beverage crates and consistently detects damage and faults that could impair the packer. Thanks to its modular design, it uses the same detection modules that are also used for empty container inspection. It takes individual quality requirements into account. This means that only containers that meet the exact requirements reach the point of sale (PoS).
HEUFT case rejector
Preventing recalls: reliable rejection of faulty crates.
Fast, careful and accurate: highest precision when detecting faults is only effective if the products in question are also removed afterwards. The device either emits a conveyor stop signal or activates the corresponding rejection system, such as the HEUFT maxi-laner, in order to remove incomplete crates from the production flow.
Fullscreen
Product monitoring and self-tests
Playing it safe: exact product tracking and regular self-tests.
Always knowing the current location of a particular product: each one is tracked precisely for this. This ensures that none remain uninspected.
Read more...
The integrated reject verification checks that each product identified as faulty is really removed. Standard test programs guarantee a regular examination of the detection performance. Network-based continuous documenting and long-term archiving of the results.
Simple brand changes
Changing automatically: automatic adjustment of the detection units.
Reliable, uncomplicated and easy: the HEUFT logic II LR carries out brand changes without manual intervention. All the parameters are adapted automatically and the height and position of the detection units adjusted by motor. Misadjustments are practically ruled out. This save valuable time and money.
HEUFT SPECTRUM II
Simply automating: universal device platform for maximum performance.
Highly automated, universal and powerful: the HEUFT SPECTRUM II ensures optimum detection and operational reliability during an in-line quality assurance for the sustainable safeguarding of product quality and line efficiency.
Read more...
The cross-system control unit with multiprocessing capability for different modules, systems and applications convinces due to its exceptional degree of automation. Brand and format changes can be carried out without manual intervention. The unique human machine interface of the universal device platform is self-explanatory. Human resources are effectively saved in this way. In-house developed hardware and software of the latest generation and a future-proof network connection achieve highest computing power and data transmission in real time. The result: maximum precision during purposeful product tracking, inspection and rejection.
Fullscreen
HEUFT reflexx A.I.
Simply detecting more: real-time image processing with artificial intelligence.
The AI discipline of machine learning for targeted object classification has been mastered by our self-developed image processing since 2010! And since then it has learned a lot: intelligent filters distinguish drops of water on the container from air bubbles in the glass and even make it possible to identify tiny defects which are hidden behind ACLs or embossings. HEUFT reflexx A.I. now also uses deep learning!
Read more...
Appropriately trained neural networks are used for example to denoise X-ray images or to find dangerous foreign objects in structured products and to reliably distinguish them from good objects which are extremely similar in their shape, size and density. With true artificial intelligence, the hardware and software from our own development and production again increases detection reliability - and minimises the false rejection rate. The smart image processing can be directly integrated into the HEUFT reflexx A.I. camera which was developed in-house and which processes and evaluates its own images directly in real time and raises the adaptive image analysis to a top level.
Fullscreen
HEUFT NaVi
Simply knowing what to do: self-explanatory audiovisual user guidance.
Intuitive, individual and audiovisual: previous knowledge is not required in order to operate the HEUFT SPECTRUM II systems reliably. The HEUFT NaVi user guidance is self-explanatory and supports the respective user step by step.
Read more...
An RFID login with user-related access rights provides an overview and makes the respective user's work simply easy: he only sees what he really needs to on the clearly arranged touchscreen user interface with a flat menu structure, integrated tutorials and precise auxiliary tools in order to fulfil his specific tasks optimally. He is supported by a virtual assistant in the course of this. She speaks to him and clearly explains what has to be done when and where. Purposeful and focussed on the essentials – the audiovisual HEUFT NaVi user guidance makes the reliable operation of HEUFT systems simply easy!
Fullscreen
HEUFT checkPoints
Simply seeing where what has to be done: trouble-free localisation.
Clear, direct and purposeful: the user can cope immediately on the rare occasions when manual intervention is needed. Because eye-catching HEUFT checkPoints make it clear at a glance exactly when it is necessary to take matters in hand in addition to the audiovisual information which the HEUFT NaVi provides.
Read more...
The orange tags not only flash on the touchscreen but also at the respective component if the worst comes to the worst. The problem is located without a long search. This saves time and human resources, shortens standstills and therefore increases productivity.
Network technologies
Networking everything: online connection for increased efficiency and quality.
Information transmission in real time, production data acquisition, line analysis and remote maintenance: networking is the answer!
Read more...
HEUFT systems have future-proof network interfaces (Gigabit Ethernet and TCP / IP) for an online connection via the Internet and the database interface (SQL / DDE) for top line efficiency and an optimum quality management with considerably faster and easier workflows. Therefore production data, shift records, productivity faults and HACCP limit value analyses are available network-wide. The result: early identification of quality and efficiency problems. The firewall protected direct connection to the HEUFT TeleService makes competent remote maintenance possible all around the clock.
Removing faulty cases:
the right rejector for all cases.
Discharging, rejecting and distributing: HEUFT rejection systems for packaging remove faulty crates, cardboard boxes, trays or shrink wrap packages reliably from the production flow. They achieve maximum performance optimally matched to their respective task with regard to precision and carefulness.
- ensuring the brand purity, unpacking suitability and quality of returned crates with empty bottles
- easy automatic brand changeover
- compact, easy to clean construction
- modular system in order to fulfil the customer's specific requirements optimally
- high processing speedreal-time image processing for maximum inspection quality with minimal false rejection rate
- intelligent combination of 3D lasers and HEUFT reflexx A.I. cameras