Full container check
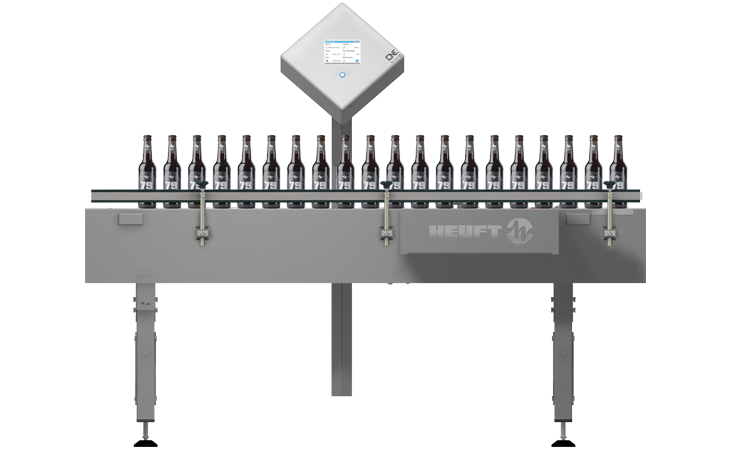
HEUFT ONE
Your affordable entry to genuine high-tech for checking full containers on a HEUFT level.
Affordable, space-saving and flexible: the extremely compact entry-level devices of the new HEUFT ONE series set standards in terms of detection accuracy, operational reliability and price / performance ratio when checking full containers in a confined space. The network-compatible complete solution fits into even the smallest installation space due to combined detection and evaluation modules (e.g. for a precise fill level, closure and label check directly on the conveyor) which are connected to a space-saving, freely positionable control unit.
Fill level detection
Finding underfills and overfills reliably: detection and analysis rolled into one.
Too little, too much or exactly right: is the filling quantity correct? The HEUFT ONE checks this reliably and precisely. Space-saving modules can be attached directly to the conveyor for this purpose. They not only deal with the detection but also the analysis and forward the results directly to the freely positionable HEUFT ONE terminal. X-ray or HF technology is available for an exact fill level check depending on the container and product characteristics. The latter technology compensates for any existing foam above the fill line. This reduces the false rejection rate on filling lines for beer or carbonated soft drinks.
Fullscreen
Closure detection
Checking the tightness: reliable detection of closure faults.
Missing, canted and unsafe: the HEUFT ONE finds closure faults such as these using a clever sensor system which can be combined together with a more complex detection technology such as a fill level detection in one and the same compact entry-level device. The fault detection and evaluation also take place here in a confined space directly at the conveyor. Therefore it makes no difference where the control terminal is along the line. Unsealed or incorrectly fitting, possibly leaking closures of equipped beverage containers are detected safely and removed reliably.
Fullscreen
Label check
Paying attention to the labels: specific examination of the presence.
Collar, body, neck or wrap-around label: there must not be any missing! The HEUFT ONE checks whether this is really the case whilst the containers are being transported directly on the conveyor by means of special sensors which make use of the different reflection characteristics of the container surface and the label. Therefore it is immediately clear when labels are missing. The danger of unlabelled bottles without information about their contents reaching the consumer has therefore been eliminated.
Fullscreen
Fault rejection
Preventing recalls: the reliable rejection of faulty containers.
Fast, careful and accurate: highest precision when detecting faults is only effective if the products in question are also removed afterwards. The single-segment and multi-segment rejection systems of the HEUFT rejector series deal with this both precisely and carefully.
Fullscreen
Optional additional functions
Detecting even more: extensions to the range of functions.
One for all: the compact HEUFT ONE can also be equipped with a powerful module for an optical marking inspection as an alternative to the different technologies for a fill level detection. The reliable detection and content-related verification of minute best-before dates, barcodes and 2D codes, part and serial numbers is achieved using in-house developed colour sensor camera technology and real-time picture evaluation. Incorrectly marked end products with wrong information about shelf life and tolerability are therefore ruled out. Can also be integrated: the proven HEUFT sonic module for an acoustic leakage check for crown corks and other metal closures.
Fullscreen
Combined detection and evaluation modules
Finding and assessing: everything at once and everything in a confined space.
Powerful, clever and space-saving: the HEUFT ONE fits into even the smallest installation spaces. Compact modules directly at the conveyor not only carry out the detection but at the same time the assessment and evaluation of the detected deviations too. The measuring results are already converted into good or faulty signals there and passed on to the control terminal. Therefore this does not have to be installed in the immediate vicinity. In fact it can be positioned anywhere along the line. The entry-level device for a reliable full container check can also be integrated into smaller filling lines without a problem.
Compact, freely positionable control unit
Accommodating flexibly: compact terminal with easy HEUFT NaVi user interface.
Location-independent, clear and very easy: it is not difficult to use the HEUFT ONE. The compact, freely positionable control terminal has a clear five inch display with intuitively understandable HEUFT NaVi user interface. Warning lights provide information about the current device status as an option. In this way an overview is kept and the full container check can be operated safely and reliably without extensive previous knowledge.
Network technologies
Networking everything: online connection for increased efficiency and quality.
Information transmission in real time, production data acquisition, line analysis and remote maintenance: networking is the answer!
Read more...
HEUFT systems have future-proof network interfaces (Gigabit Ethernet and TCP / IP) for an online connection via the Internet and the database interface (SQL / DDE) for top line efficiency and an optimum quality management with considerably faster and easier workflows. Therefore production data, shift records, productivity faults and HACCP limit value analyses are available network-wide. The result: early identification of quality and efficiency problems. The firewall protected direct connection to the HEUFT TeleService makes competent remote maintenance possible all around the clock.
HEUFT rejector
Removing faulty products: the right rejector for all cases.
For example, the single-segment HEUFT flip and HEUFT mono rejectors as well as the multi-segment HEUFT DELTA-FW and HEUFT DELTA-K systems are ideally suited for the reliable rejection of faulty full containers.- space-saving full container check on a HEUFT level
- genuine high-tech at an unbeatable price / performance ratio
- compact complete solution comprising innovative detection technologies
- in-house developed hardware and software and proven procedures for highly precise product tracking, inspection and fault rejection
- easy to integrate stand-alone system with flexible detections directly at the conveyor connected to a freely positionable control unit
- reliable quality check of up to 72,000 filled beverage containers per hour