空瓶检测
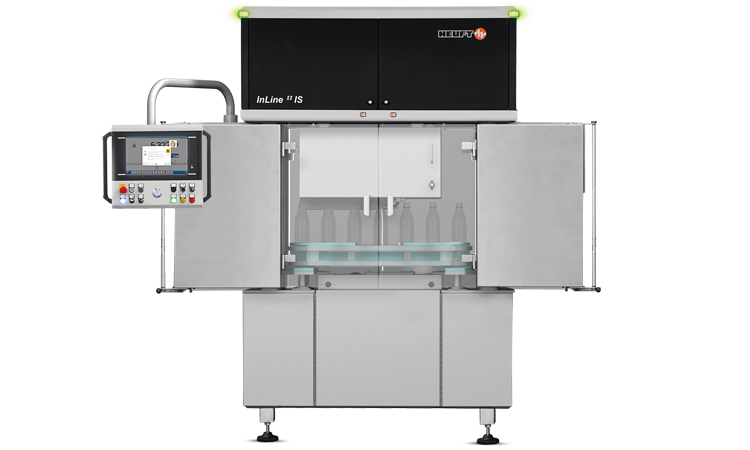
HEUFT InLine II IS
打造精品标准:真正的高科技,实现连续的空瓶检测。
高度自动化、功能强大且操作可靠:新标准HEUFT InLine II IS 用于全面的空瓶检测。HEUFT InLine II IXS 的所有的优势都转移到了全新一代结构简洁的系统中,该系统在卫生和维护方面进行了优化。结论就是:功能强大,配置齐全,操作方便的空瓶检测设备达到了新的水平,明确了技术发展的状态。优质成为标准!
进瓶检测
确保瓶型纯度:预分拣进瓶检测
缺陷、偏差和外来瓶:HEUFT InLine II IS 可以配置不同的进瓶检测技术包括剔除系统,这样此类瓶子就不会首先进入,从而影响检测性能和整个灌装生产线。因此,在真正的空瓶检测开始前我们要进行特定的预分拣以保证同类产品的供应:只有可以被检测和灌装的合适的空瓶才能无障碍通过。这不仅保证了生产质量,同时也提高了整个生产线的效率和生产力。
光学瓶底检测
覆盖一切:可靠地检测空瓶瓶底的安全风险。
薄膜、烟头和昆虫:系统能够进行光学的瓶底检测,以便可靠地检测此类低密度异物。数百个特殊排列的LED,可灵活控制,确保每个瓶型的瓶底区域从中心到外边缘都能被均匀照射。如此智能地定位高性能照相机,能使透明和反射的缺陷显而易见——无论它们在哪个方位。并且玻璃碎片、缺口和裂缝也能在持续的全面瓶底检测中被清晰地识别。HEUFT reflexx A.I 图像处理系统实时结合分析检测图像,进行具体的自动寻找参数程序。
Fullscreen
瓶口和螺纹检测
发现缺陷和裂缝:瓶口处的安全
瓶口的缺陷、裂缝,铁锈环,污染物和螺纹处的缺陷:此系统拥有独创性的技术利用光学检测瓶口和螺纹,以便在此类缺陷危害产品安全前发现它们。它不仅能覆盖整个密封面,还能覆盖下面的缺口/螺纹。创新的LED照明和照相机技术能够进行进一步的密封面检测:集成的安全环颜色检测,甚至可以使热裂纹,张力裂纹和其他没有明显材料损失的缺陷变得可见。下方区域内被检测到的污染物和缺陷的精度与瓶口内侧壁区域以及螺纹圈上的一样高。这保障了瓶口区域周围的完整性,就和待灌装空瓶的密封性一样。
Fullscreen
360°侧壁检测
全方位检测:连续全面的检测。
污染、缺陷、夹杂物或者裂纹:任何希望可靠检测此类质量缺陷的非常有必要拥有全面检测。在进行空瓶的所有侧壁检测之后,所有区域必须全部覆盖。HEUFT InLine II IS 能够通过使用最多两组双倍分辨率的四侧壁检测模块实现这个功能。几个高性能照相机能够提供八张清晰的视图,覆盖整个瓶子容积360°以上。,空瓶因此有目的地旋转并且使用精确的伺服技术 在每个检测站点进行最佳对齐。同时,均匀的照明保证了检测图像没有阴影和反射。这些图片由HEUFT reflexx A.I 结合并进行实时分析。在此过程中,高性能的图像处理系统能够可靠地区分无害容器结构和真正的缺陷并进行特定自动寻找参数程序。
Fullscreen
残留液检测
追踪碱液、油和清漆:有效防止产品被污染。
苛性碱液、油或清漆:即使是少量的此类产品也会严重威胁到终端产品的安全和消费者的健康。该系统有两种不同的方法在灌装前检测并将有问题的空瓶移除:它可以使用高频技术检测残留碱液,红外线检测油和清漆。和重新设计的HEUFT InLine II IS 的所有检测模块一样,残留液检测单元完全集成,安全封闭并由电机调节。这也适用于之前必须安装在检测设备外输送带上的HEUFT fluid。由于空瓶检测设备的新结构,简洁的残留液检测模块现在也能直接在设备中展示它令人赞叹的精度。
Fullscreen
剔除不合格包装
减少召回:剔除不合格容器的可靠性
快速、平稳、精准:只有当不合格产品从生产线上被剔除时,检测的高精度才有意义。HEUFT rejector系列的单段或多段剔除系统能精准且平稳地实现这一点。
Fullscreen
确切的产品追踪和定期的自我测试
产品监控和自我测试使其安全:确切的产品追踪和定期的自我测试。
始终清除某一特定产品的当前位置:每一个都被精确追踪,并确保没有未经检测的。集成的剔除确认能够检查每一个被认定为错误的产品准确地被移除。标准的测试程序能确保检测性能的定期检查。基于网络连续记录和长期归档结论
Fullscreen
简单的瓶型更换
自动更换:伺服控制可调节输送带。
精确的伺服技术不仅仅能对瓶子进行特定旋转和准确的微调以实现在智能输送带上持续全面的检测,而且在瓶型更换过程中,还能根据改变的瓶型模式调节输送皮带的高度和宽度。这同样适用于所有检测的定位。根据清晰重复的瓶型调整,这完全是全自动的。因此,这减少了人工干预的需求,节省了人力资源,不仅节省了时间还节约了资金:可持续地减少由于长时间的人力更换而导致的效率和生产力损失。
可选的附加功能
检测更多:功能扩展。
模块化设计的HEUFT SPECTRUM II 系统可随时扩展。根据性能和质量要求可选择两个或者四个侧壁检测。特殊的磨损检测可用于那些待灌装的可回收瓶。该功能可与剔除率控制结合,只有在生产情况允许的情况下,才移除磨损不严重的缺陷瓶。隐藏在彩色商标后面的缺陷和污染物通过可随时集成的ACL检测变得可见。HEUFT InLine II IS 还能提供不同的选项用于瓶口和螺纹检测——从密封面的彩色环检测到椭圆度检测。除了那些已经集成在设备中的多余保护,残留液检测可以连接到输送带上。
HEUFT SPECTRUM II
简单自动化:性能最大化的通用设备平台。
高度自动化、通用和强大:HEUFT SPECTRUM II能够确保在线检测过程中最优化的检测和可靠的操作,以持续保障产品质量和生产线效率。高度自动化及多重处理能力的跨系统控制单元用于不同模块、系统和应用。无需人工干预就可以进行瓶型和结构更换。通用平台独一无二的人机界面是不言自明的,有效地节约了人力资源。内部研发的新一代硬件和软件以及具有前瞻性的网络连接能够达到最大的计算机处理能力和实时数据传输。结论就是:有目的地产品追踪、检测和剔除过程中能达到最大精度。
Fullscreen
HEUFT reflexx A.I.
只需识别更多: 人工智能实时图像处理。
自 2010 年以来,我们自主开发的图像处理技术已经掌握了用于目标对象分类的机器学习这一人工智能学科!从那时起,它已经学会了很多:智能过滤器可以区分容器上的水滴和玻璃中的气泡,甚至可以识别隐藏在 ACL 或浮雕后面的微小缺陷。HEUFT reflexx A.I. 现在还使用了深度学习技术!
经过适当训练的神经网络可用于去噪 X 射线图像或在结构化产品中发现危险异物,并将其与形状、大小和密度极其相似的良好物体可靠地区分开来。通过真正的人工智能,我们自主研发和生产的硬件和软件再次提高了检测的可靠性,并将错误剔除率降至最低。智能图像处理可直接集成到 HEUFT reflexx A.I. 相机中,该相机由公司内部开发,可直接实时处理和评估自身图像,并将自适应图像分析提升到最高水平。
Fullscreen
HEUFT NaVi
轻松知道该怎么做:不言自明的试听用户指南。
直观、独特和试听:无需为了可靠操作HEUFT SPECTRUM II系统而实现学习。HEUFT NaVi用户指南是不言自明的,能够分别一步步地支持用户。带有用户相关权限的RFID登录系统提供了一个概述,使得每个用户的工作都变得简单轻松:用于能在清晰排版的触摸屏用户界面上看到他真正所需要的,通过一个平面菜单结构,综合的教程和精确的辅助工具以最佳的满足他的要求。在这个过程中,他将受到虚拟助理的支持。她会与其说话,并详细地跟他说明何时何地做什么。有目的地关注重点:试听的HEUFT NaVi用户指南使得可靠地操作HEUFT系统变得轻松简单!
Fullscreen
HEUFT checkPoints
简单地查看哪里需要做什么:无故障定位。
清晰、直接和有目的性:用户可以在需要人工干预的情况下立即处理这一罕见情况。因为除了HEUFT NaVi提供的试听信息,醒目的HEUFT checkPoints一下便能马上清晰准确地判断何时必须着手采取行动。万一出现最糟的情况,橙色标签不仅在触摸屏上,同时也在各个部件上闪烁。它的位置不需要长时间搜索。这节省了人力资源,缩短了停机时间从而增加了生产力。
网络技术
全面联网:在线连接以提高效率和质量。
信息实时传输,生产数据采集,线路分析和远程维护:联网就是答案!HEUFT系统拥有前瞻性的网络界面(千兆以太网和TCP / IP)用于通过网络和数据库界面(SQL / DDE)进行在线连接,以通过非常快速和简单的工作流程达到最高的生产线效率和最优的质量管理。因此,可实现全网络可用生产数据、交班记录、生产力错误和HACCP限值分析。结论是:尽早发现质量及效率问题。防火墙能保护与HEUFT TeleService的直接连接以实现全天候提供可靠的远程服务。
HEUFT CleanDesign
Cleaning quite simply: hygiene-optimised construction.
Accessible, clean and safe: its HEUFT CleanDesign predestines the system for use in hygienically sensitive areas.
Read more...
Sloping surfaces facilitate cleaning and prevent the accumulation of stubborn dirt. Special channels and openings allow the liquids required for cleaning purposes to be drained off completely. Consequently dangerous germs and bacteria have no contact surface whatsoever. Specially constructed casings and doors create optimum accessibility. The electronics are totally encapsulated. Sensitive areas such as the inspection units are dust-proof and protected against contact as well as water jets.
But that is not all by any means. The HEUFT InLine II IS scores points with a further optimised construction: open, easily accessible and with neither frame nor machine table its new HEUFT CleanDesign reduces cleaning and maintenance. All the detection modules are safely enclosed, adjustable by motor and fully integrated. A new, extremely slim conveyor / drive concept nevertheless ensures that the linear machine has compact dimensions for the straightforward integration into tight installation positions.
Fullscreen
HEUFT rejector
剔除错误的产品:适合所有箱子的剔除器。
For example, the single-segment HEUFT mono and HEUFT flip rejectors as well as the multi-segment HEUFT DELTA-FW and HEUFT DELTA-K systems are ideally suited for the reliable rejection of faulty empty bottles. Up to four rejection systems can be connected to the HEUFT InLine II IS. This also makes a rejection possible which is sorted according to the fault type.
- 每小时持续完整检测多达84000个空瓶的新标准
- 将先进的技术从HEUFT InLine II IXS 优质的设备转移到全新的简洁优化结构中,便于维护
- 优越的光学和传感器检测技术
- 优化的传送和精准的瓶子对齐,用于侧壁检测过程中双倍分辨率的超360°覆盖范围
- 更精确地光学瓶底,瓶口,密封面,螺纹和缺口检测
- 所有检测单元完全集成,带有安全保护罩和全自动调节
- 可通过添加模块直接扩展功能,诸如磨损环检测或者ACL检测等可以额外集成
- 高度自动化的HEUFT SPECTRUM II 平台带有自解释的HEUFT NaVi 用户指南用于扩展的视听逐步辅助——可灵活旋转的鹅颈管控制终端,可在两侧使用
- 实时图像处理系统具有学习能力和自动寻找参数功能
- 使用方便的HEUFT CleanDesign 既没有框架也没有平台的只需简单的清洁和维护
- 在线连接远程维护和生产数据采集